素材・用途別事例
電子部品材料
焼成前は微細化で固相反応を促進!
焼成後はマイルド分散で粒子の特性を維持したまま解砕
微細化の目的
- 焼成温度の制御
- 数種類の粒子を均一に混合および微細化
- 製品の小型化
用途・材料名
積層セラミックスコンデンサー(チタン酸バリウム・ニッケル)、フェライト(酸化鉄)、インダクタ、導電ペースト、サーミスタ、バリスタ、ノイズフィルタ
求められる機能
- チッピングの抑制
- コンタミネーションの低減
- 高濃度による生産量の増加
推奨のポイント
- 乾式ビーズミルSDAは溶媒を使わずミクロンサイズまで微細化ができます
- MAXナノ・ゲッターは粒子の形状を変えずに一次粒子まで分散(マイルド分散)ができます
技術データ
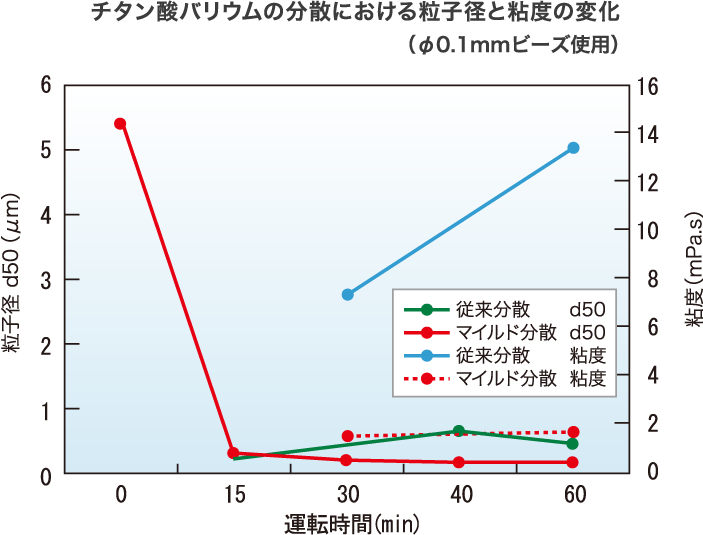
[データ解説]
従来機による分散と比較すると、ナノ・ゲッター(DMR)によるマイルド分散は粘度が急上昇することなく、マイクロビーズを安定して使用することができ、安定的に粒径を小さくしていくことが可能です。
[ 工程例 ]
原材料配合
乾式湿式 混合粉砕(エコ粉砕)
- お困り事より微細な粉を製造するためのコストが高い
- 解決乾式+湿式の組み合わせで消費電力削減
“エコ粉砕”とは乾式ビーズミル(ドライスター)と湿式ビーズミル(ムゲンフローMGF)の組み合せにより、エネルギー効率を飛躍的にアップさせ、省エネ粉砕を実現する新しいシステムです。
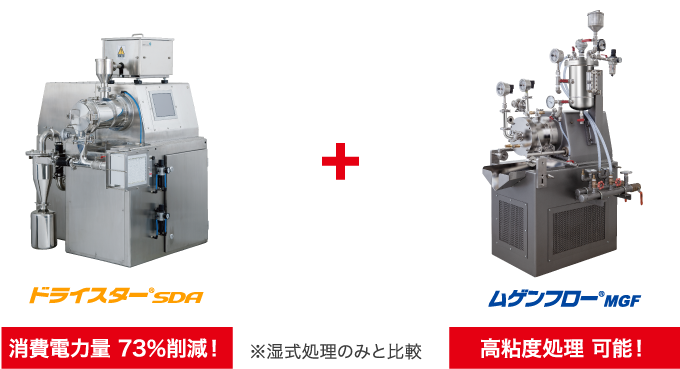
乾燥
仮焼成
乾式 解砕
- お困り事目標粒度まで微細化するのに長時間の処理が必要
- 解決乾式ビーズミルで所定の粒度まで効率よく微細化!!
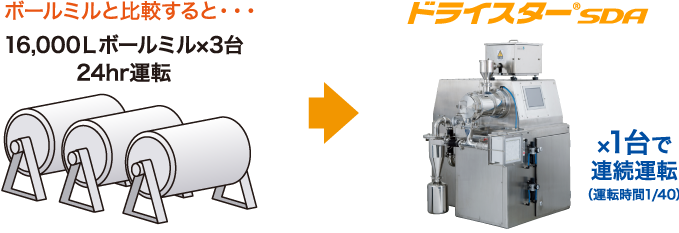
- さらに
- 機械台数 1/3
- ビーズの量 1/60
- 設備コスト 1/2
- 設置面積 1/7
仮焼粉
湿式 混合粉砕(分散)
- お困り事チッピングが発生してしまい性能が十分に発揮されない
- 解決マイルド分散® 技術
マイルド分散®とは、一次粒子のサイズ、形状、結晶構造、表面状態などを維持したまま分散させる技術です。
◎分散事例 対象物:酸化チタン
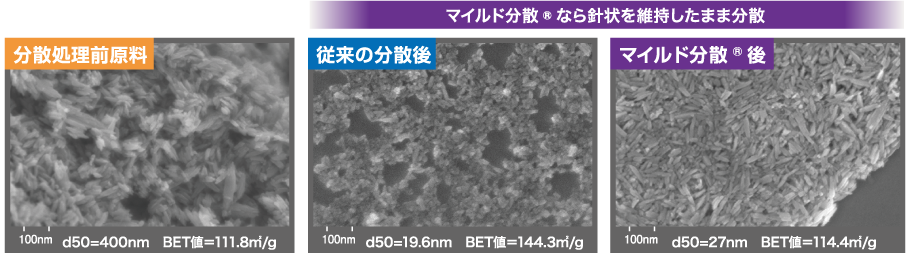
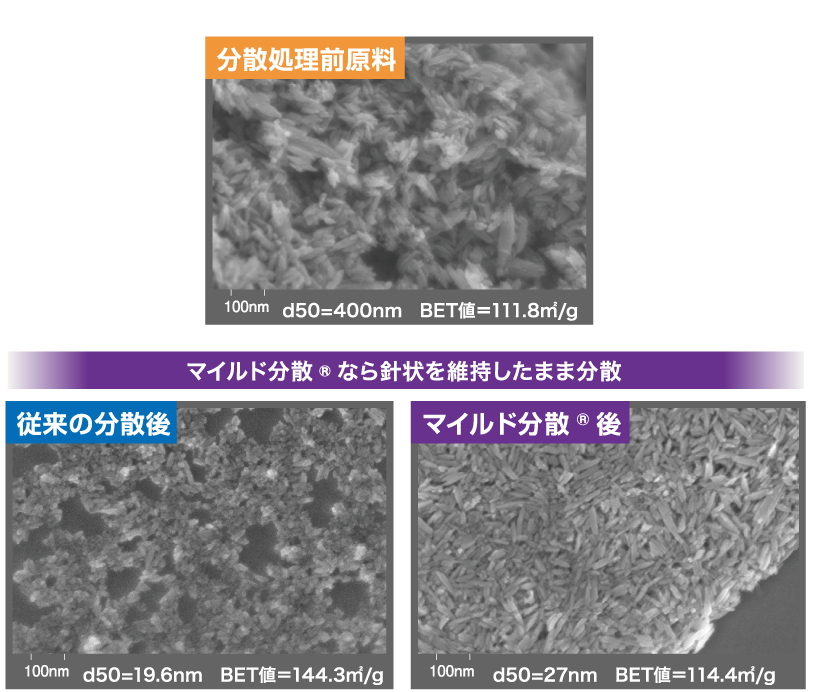
◎マイルド分散®のメリット
- ・粒子の特性維持
- ・再凝集抑制
- ・分散剤量を削減
- お困り事微小ビーズを使ってスケールアップをしたい
- 解決大量生産実績多数のMAXナノ・ゲッター® で解決!!
二軸構造なのでビーズの運動を制御する能力や分離能力が高く、今まで微小ビーズ(φ0.015mm)で運転が困難だったスラリーでも安定運転が可能。
生産機へのスケールアップも可能であり、大量生産の実績多数!!
◎MAXナノ・ゲッター®の特長
- ・安全運転
- ・大量処理

◎理想的なビーズの動きを実現『らせん層流』
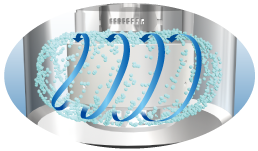
◎粉砕室内のエネルギーが均一で「分散」に最適な形状
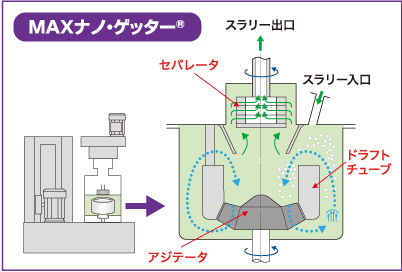
乾燥
調合原料
成形
焼成